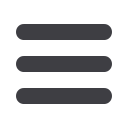
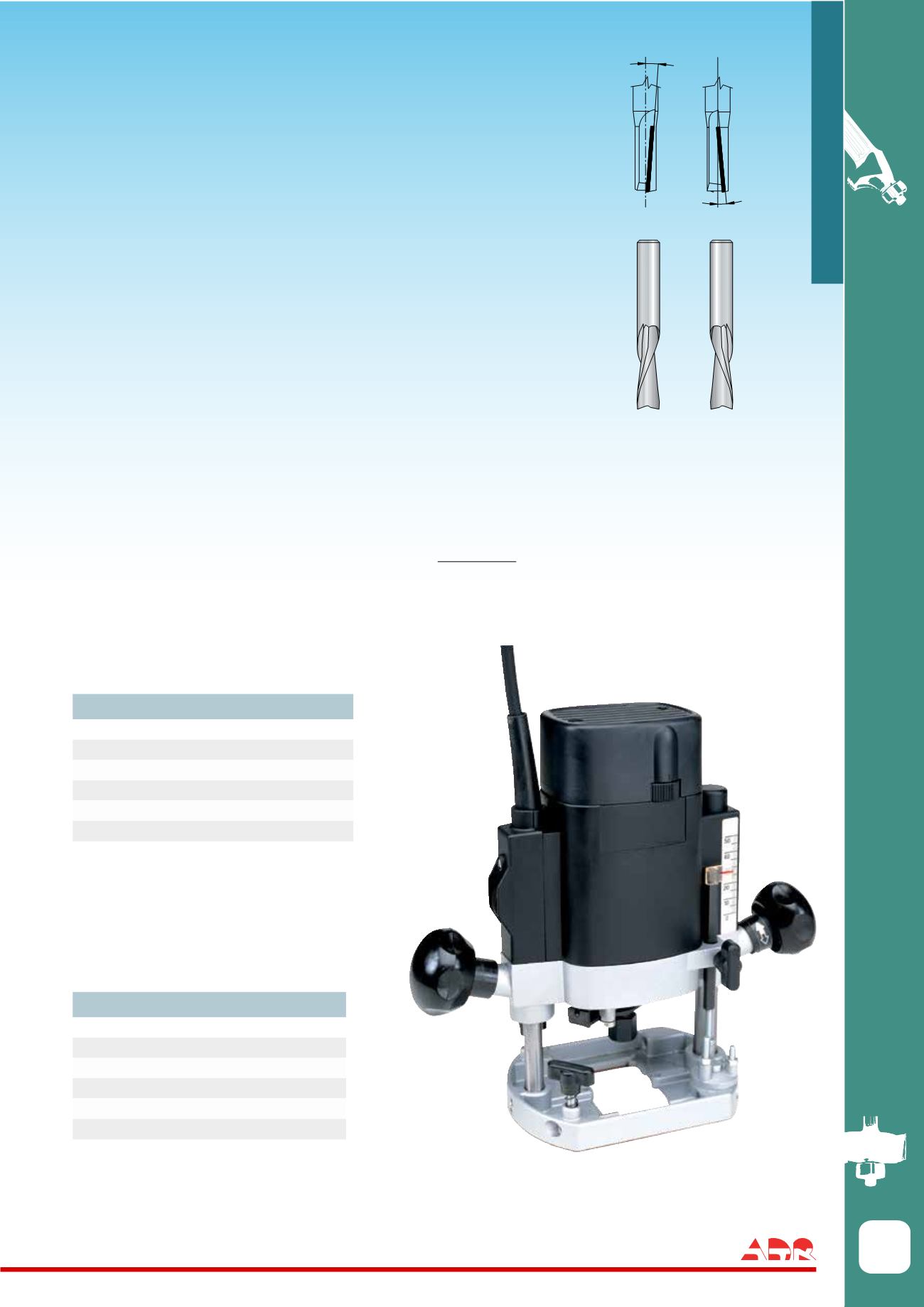
כרסמים לרוטר ושקענים
668
03-9529998 :
ראשל”צ טל
1
אדר יבוא ושיווק פרזול בע”מ רחוב דוד רזיאל
www.adrtrading.co.il03-9511511 :
פקס
84
Technical Information
About Cutting and Router Speeds
We are often asked about recommended cutting speed for routing. The answer is complicated. The maximum allowed cutting
speed for Carbide Router Bits depends on many factors such as:
1. Material type and hardness.
2. Stability of the system: machine, chuck, work piece.
3. Tool length and depth of cut.
The general formula for calculating Router speed (n) is:
n
=
n
= router speed in RPM
V
= cutting speed in meter/sec.
ØD
= router bit’s diameter in mm
π
= 3.14…
RECOMMENDED CUTTING SPEED
V
x 60 x 1000
π
x
ØD
This speed is not always practical. Taking into consideration the
speed and the power of Router machines that are available in the
market, we suggest the following router speeds in terms of RPM
(Revolutions Per Minute).
Ø
D
n
(RPM)
Up to 25mm (1”)
30,000
Up to 35mm (1-5/8”)
28,000
Up to 50mm (2”)
20,000
Up to 65mm (2-1/2”)
18,000
Up to 80mm (3-1/4”)
16,000
Up to 95mm (3-3/4”)
12,000
Material
V
Softwood
60 - 90
Hardwood
50 - 80
Chipboard
60 - 80
Plywood
60 - 80
MDF
40 - 60
Laminates
40 - 60
SUGGESTED ROUTER SPEED - RPM
Shear Angle
Straight Shear Bits and Solid Carbide Spiral Bits are made with negative - “down shear”
or positive - “up shear” angle of the cutting edges. By spreading the cutting action over a
larger part of the tool, they produce smoother cuts with less energy and less vibration, than
standard Straight Bits. This is the reason why profile router bits and cutters are usually
made with an up shear angle, and this is also the advantage of straight spiral bits. Straight
Shear Bits are a compromise between the standard Straight Bits and the expensive,
industrial Solid Carbide Spiral Bits.
“Up shear”
/ Upcut geometry pulls the chips from the working area, allowing deep
grooving and higher feed rates.
“Down shear”
/ Downcut geometry directs chips towards the work piece and results
smoother cut and cleaner edge of laminated boards.
The combination of Upcut and Downcut design, also called: “Compression”, is suitable for
perfect cutting with clean edges of double-sided laminated materials.
Up
Down
Up
Down
Single
Flute
Stagger
Flutes
2 Flutes 4 Flutes
Up Shear
Down Shear
Up
Down